
Guild.
Jean-François began his demonstration with a small trembleur, which was done between centers.

Here is the small trembleur he turned out of hard maple. This was done by turning a number 2 morse taper for the headstock, which was jammed into the headstock. The other end was initially supported by the tailstock. He worked the topmost 2 inches first and turned it off the tailstock end. From that point on the trembleur was supported by his right hand as he used the bedan or spindle gouge in his left hand.
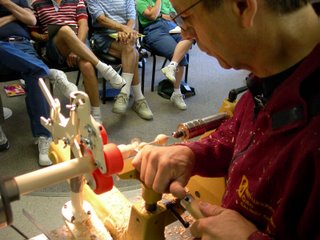
The second project of the day was a long trembleur. This needed a spindle steady rest, first a one-way style one with wheels and then with the addition of a string steady rest.
The piece was held with pin jaws in a one-way stronghold chuck. Jean-François again worked two inches at a time from top to bottom.

Here is the string steady rest all set up and ready to go. The string is first tied off in the upper left hand corner and then wound around the lower right hand nail, then over to the upper right hand nail, down to the lower left corner and tied off at the upper right hand corner. The strings are tied together in the middle from side-to-side and top-to-bottom. The steady rest is shown in more detail below.

The top part is attached in such a way that it can be pivoted out of the way as the trembleur is removed from the lathe. Jean-François told us about the trembleur he made that was as tall as his height. This one required 24 string steady rests and two people to remove it from the lathe - one to cut the strings and move the steady rests away from the spindle and the other to slide a glass tube along the length to capture and support the trembleur.

"Here - catch it!" We did get to look at each of these turnings closely as they were passed around the room.

Here's the one from today's demonstration. Jean-François kept apoligizing for the poor quality of his demo pieces, but I think everyone was suitably impressed by his work.
Jean-François told us that he thinks practicing on trembleurs is a good way to improve one's turning skills. "Everything else is easy."

Next it was on to multi-axis turning; first, between centers and then with the Escoulen chucks.
This one is on three centers. Looks pretty wild as the extreme ends are between centers. He started this one in the middle on axis 1, then did axis 2, axis 3, and then back to axis 1.

This one had seven axes, and it was started at one end and progressed along each axis to the other end.

Setting the tool rest is pretty critical as is working with tools in a long handle since the cutting edge is far off the tool rest for most of the cuts.

As the piece is spinning, the shadow lines are the areas where the shape will emerge. I'm looking forward to taking Jean-François' five-day hands-on class this week. I can't wait to try this technique.

Here are the two multi-axis turnings that were done between centers. Jean-François numbered the one on the left so we could see which axis was used for each section.
"I numbered them in French, but you should be able to read them," he said.
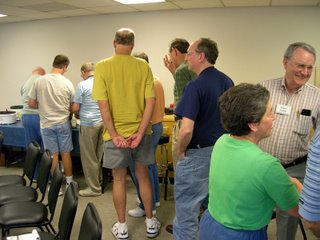
We had a lunch break after the between centers session for the morning.
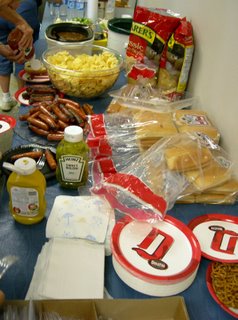
Bar-b-que on a nice summer's day, combined with an excellent woodturning demonstration. What could be better than that?
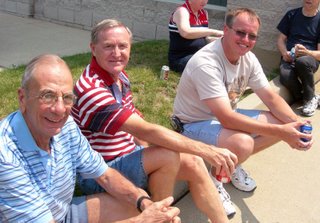
These guys looked happy.

Here's Jean-François Escoulen's work table.

Here are some of the tools he used: two different sizes of bedans and spindle gouges. Notice the double bevel on the gouges? That's to help with the tight corners on multi-axis turnings. The bedans are used for most of his cuts - another technique I'm looking forward to learning this coming week.
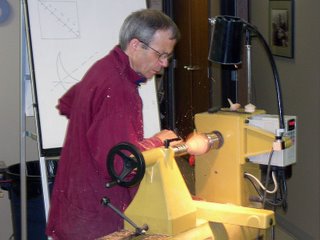
This project is a multi-axis spoon. He's using his small ball chuck. I'll try to take some detail pics during the hands-on class to show the parts and how they're set-up for this type of work.

Hollowing out the bowl of the spoon is a bit of a challenge with the stem spinning around. The spoon is an end-grain turning, so the cuts are from the center toward the outside for the hollowing process. That makes it a bit easier to deal with the stem.

Here's the finished spoon.

The last project of the day done between centers was one of his classic multi-axis boxes. This was really fun to watch.

Jean-François apologized for how thick the finial is, but he was limited by his drill bit size. He had several offers to take that ugly box off his hands. . .

The last hour of the demonstration focused on multi-axis face-plate turning. Jean-François has also designed a couple of chucks for this type of work. The axis can be changed from side-to-side and front-to-back. The ball part of the chuck is threaded onto the headstock rather than for holding the wood.
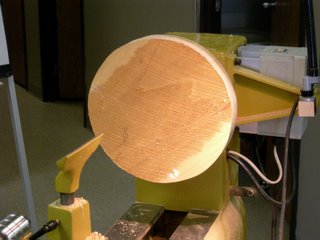
The project starts out on center and looks like any regular ol' platter.

The bowl part of it is turned off-center and then the grooves are made by changing the axis front-to-back. Lots of possibilities come to mind with this technique, but it's probably not something I will be exploring anytime soon.
I'll try to take a lot of pictures this week and update the blog as I have time.
No comments:
Post a Comment